Chinese glue website releases epoxy resin 123,Adhesive manufacturer
glue manufacturersEpoxy resin refers to a general term for a type of polymer that contains two or more epoxy groups in its molecules. It is the condensation product of epichlorohydrin with bisphenol A or polyols. Due to the chemical activity of epoxy groups, various compounds containing active hydrogen can be used to open the ring, cure and crosslink to form a network structure, making it a thermosetting resin. Bisphenol A-type epoxy resin not only has a large production volume and a wide variety, but also new modified varieties are constantly increasing, and the quality is constantly improving. Application of epoxy resin in coatings: Epoxy resin accounts for a large proportion of applications in coatings, and it can be made into various varieties with different characteristics and uses.
Common characteristics of epoxy resin:
1. Excellent chemical resistance, especially alkali resistance.
2. The paint film has strong adhesion, especially to metals.
3. It has good heat resistance and electrical insulation.
4. The paint film has good color retention. However, the weather resistance of bisphenol A-type epoxy resin coatings is poor, and the paint film is prone to powdering, loss of gloss, and incomplete in outdoor environments, making it unsuitable for outdoor coatings and high decorative coatings. Therefore, epoxy resin coatings are mainly used as anti-corrosion paints, metal primers, and insulation paints, but coatings made of heterocyclic and cycloaliphatic epoxy resins can be used outdoors.
Chinese glue website releases epoxy resin 123,Adhesive manufacturer
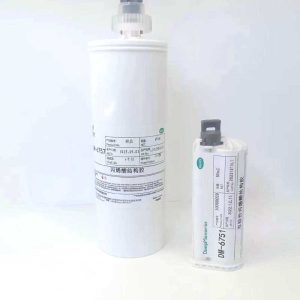
Adhesive application:
Epoxy resin not only has poor adhesion to non-polar plastics such as polyolefins, but also to various metal materials such as aluminum, steel, iron, and copper; Non metallic materials such as glass, wood, concrete, etc; Thermosetting plastics such as phenolic, amino, unsaturated polyester, etc. have excellent adhesive properties, hence they are known as versatile adhesives. Epoxy adhesive is an important type of structural adhesive. Electronic appliances: Due to its unique advantages such as high insulation performance, strong structural strength, and good sealing performance, epoxy resin has been widely used in the insulation and packaging of high and low voltage electrical appliances, motors, and electronic components, and has developed rapidly.
Mainly used for:
1. Casting of insulation packaging components for electrical appliances and motors. Manufacturing of fully sealed insulation packaging components for high and low voltage electrical appliances such as electromagnets, contactor coils, transformers, dry-type transformers, etc. It has achieved rapid development in the electrical industry. From normal pressure pouring and vacuum pouring, automatic pressure gel forming has been developed. Epoxy insulation coatings, insulation adhesives, and electrical adhesives are also widely used. What is epoxy resin material? Epoxy resin anti-corrosion material is mainly composed of the following materials.
One is epoxy resin
A general term for polymers containing epoxy groups, mainly suitable for media with low corrosiveness. They have outstanding alkali resistance and can withstand general acid (except hydrofluoric acid) corrosion. The demand for epoxy resin in foreign anti-corrosion markets has greatly reduced, mainly due to the rapid development and variety of unsaturated polyester resin in the field of anti-corrosion resin. In the domestic market, due to the late start of unsaturated polyester resin, epoxy resin is still one of the main resin varieties in the field of anti-corrosion. The main characteristics of epoxy resin are high bonding strength, low shrinkage rate, high product brittleness, and high price. The resin cured at room temperature should not exceed 80 ℃ for use;
The second is the curing agent for epoxy resin
There are several types of compounds, including amines, anhydrides, and resin compounds. Among them, amine compounds are the most commonly used, which can be further divided into fatty amines, aromatic amines, and modified amines. Due to the high toxicity and odor of compounds such as ethylenediamine, meta phenylenediamine, phenylenediamine, polyamide, and diethylenetriamine, they are gradually being replaced by non-toxic and low toxicity new curing agents (such as T31.590, C20, etc.). These curing agents can cure wet substrates and even underwater, so they are increasingly attracting people’s attention and praise;
The third is diluent,
The dilution of epoxy resin usually uses non reactive diluents such as ethanol, acetone, benzene, toluene, xylene, etc. The two non reactive diluents can be mixed, and sometimes active diluents such as epichlorohydrin butyl ether, epichlorohydrin phenyl ether, and diglycidyl ether are also used to reduce the shrinkage rate, porosity, and cracking of the cured product; The fourth is plasticizers and toughening agents. Simple epoxy resins are brittle, have poor impact toughness, flexural strength, and heat resistance after curing. Plasticizers and toughening agents are commonly used to increase the plasticity, improve toughness, flexural strength, and impact toughness of the resin; The fifth is the filling material, which includes powder, fine aggregate, coarse aggregate, and glass flakes. Adding appropriate filling materials can reduce the cost of the product and improve its performance. The amount of filling material used in the adhesive solution is generally 20-40% (by weight) of the resin amount. When preparing putty, the amount can be relatively large, usually 2-4 times the resin amount. Commonly used powders include quartz powder, porcelain powder, as well as graphite powder, diabase powder, talc powder, mica powder, etc. The usage method of epoxy resin is to add and use it according to the user’s formula, and its long-term indoor storage performance is stable at 5 ℃ -35 ℃. Purchasing epoxy will come with a curing agent. The amount of curing agent poured into the epoxy resin is generally 1 barrel: 1 barrel (the manufacturer usually provides packaging with a suitable ratio, which is definitely larger for epoxy and smaller for curing agent), but the ratio may vary slightly depending on temperature and other factors. Then stir it evenly. The ones I come into contact with are 4L epoxy containers for ships, which are mixed using an electric drill (with mixing blades installed). This is a technical task, no bubbles should appear, it needs to be stirred evenly, and the time should not be too long. For a 4L container, it is generally better to keep it within 2 minutes. Then it’s pouring, welding baffles in the designated area, sealing the gaps to prevent them from flowing out. Then just pour the mixture directly into the designated area.
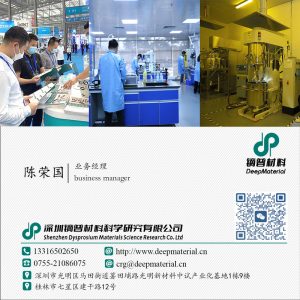