Adhesive website polymer battery cell surface insulation adhesive DM907 low viscosity UV curing adhesive
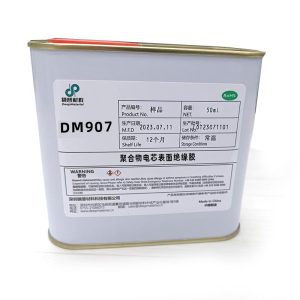
Overview of Polymer Cell Surface Insulation Adhesive Products
DM901 is a low viscosity UV cured surface insulation adhesive for water-cooled panels that can undergo secondary curing. Therefore, even in shaded areas, optimal performance can be ensured. Thin layer coatings can almost instantly solidify, have good film-forming properties, and have good adhesion to various metal, ceramic, and glass filled epoxy resin surfaces. This formula is based on solvent-free modified polyurethane acrylate, specifically designed for surface insulation of water-cooled plates. The product can be used to protect the surface of water-cooled plates from environmental erosion, thereby improving and extending their service life, ensuring safety and reliability of use.
Product information of polymer cell surface insulation adhesive
appearance | Transparent liquid | ||
consist of | one-component | ||
Viscosity | Low viscosity | ||
Curing Method | UV moisture curing | ||
Product Features | Fast curing speed, able to cure in shaded areas Has good electrical stability under different temperature and humidity conditions |
||
application | Used for surface insulation of polymer battery cells |
Physical properties of surface insulation adhesive for polymer battery cells
index | unit | numerical value | |
colour | / | Transparent liquid | |
Viscosity@25℃ | mPa.s | 75 | |
Viscosity@25℃ | g/cm3 | 1.05 | |
Curing conditions@600mW/cm2 | s | 10 | |
Moisture curing conditions in shaded areas | Days | 3 | |
hardness | Shore D | 80 | |
thermal conductivity @25℃ | W/(m.K) | 0.28 | |
Dielectric constant/loss@1MHz | – | 2.75/0.013 | |
Volume resistivity | Ω.cm | 2.8×1016 | |
Surface Resistivity | Ω | 3.1×1016 | |
dielectric strength | Kv/mm | 20 | |
operation temperature | ℃ | -40~135 |
Instructions for using polymer cell surface insulation adhesive
1. This product is sensitive to light. During storage and handling, exposure to the external environment and artificial light should be minimized as much as possible.
2. When spraying this product, a black rubber hose and a needle with UV protection are required. To achieve optimal performance, all surfaces in contact with the material before spraying should be clean and free from solder residue, grease, release agents, or other contaminants.
3. Apply adhesive to one of the bonding surfaces and assemble immediately. When exposed to liquid adhesives, crystalline and semi crystalline thermoplastic materials should be checked for the risk of stress cracking.
Excessive uncured adhesive can be wiped off with organic solvents.
5. The curing speed depends on the intensity and distance of the light source, the required curing depth or thickness, and the transmittance of the components between the material and the light source.
6. Oxygen may inhibit surface curing. Surfaces exposed to air may require high-intensity ultraviolet radiation to produce dry surface curing. Filling the solidification area with inert gas (such as nitrogen) can also reduce the oxygen inhibition effect.
7. Cooling systems should be provided for temperature sensitive substrates, such as thermoplastic materials. Before testing, the bonded parts should be cooled down before conducting any load or electrical tests.
Storage of surface insulation adhesive for polymer battery cells
Sealed and stored in a dark and dry environment at 20-30 ℃, with a shelf life of 6 months. Do not remove materials from their original packaging during use. Please do not repack the materials into their original packaging.
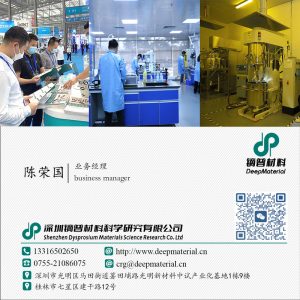